Table of Contents
ToggleScope of Charcoal Making Methods for CarbonizationÂ
- Producing charcoal from agricultural biomass on a farm can be a practical way to manage waste and create a valuable resource for soil enrichment, energy, or as a component in biochar.
- The scope of charcoal-making methods for carbonization encompasses various techniques that differ in efficiency, cost, environmental impact, and quality of the resulting charcoal. Here’s an overview of commonly used methods and their scope in terms of performance, scalability, and applications:
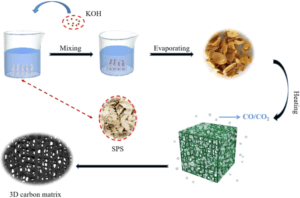
Traditional Pit and Earth Mound Kilns
- Description: These methods involve placing biomass in a pit or covered mound with limited oxygen. They’re among the oldest and simplest methods.
- Scope:
- Low Cost, Low Efficiency: They are inexpensive and accessible but have low efficiency (yield is around 15-25% of initial biomass).
- High Emissions: Emit significant smoke and pollutants due to incomplete combustion.
- Small-Scale Suitability: Best for rural, small-scale production where resources are limited.
- Quality Variability: Charcoal quality is inconsistent due to difficulty in controlling airflow and temperature.
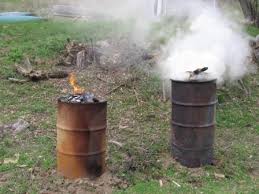
Metal Drum Kilns (Oil Drum Method)
- Description: This method uses a metal drum with ventilation holes, allowing limited oxygen for controlled burning of biomass.
- Scope:
- Improved Control: Offers better control over oxygen flow compared to traditional kilns, producing more uniform charcoal.
- Portable and Affordable: Suitable for small-scale use and portable, making it popular for farm-based or community-level production.
- Moderate Efficiency: Higher efficiency than pit methods, with charcoal yield around 25-30%.
- Environmental Impact: Still produces some smoke, but improved design (like double-barrel configurations) can help reduce emissions.
Retort Kilns
- Description: Retort kilns have a dual-chamber design, where heat in one chamber drives carbonization in another, with released gases partially sustaining the process.
- Scope:
- High Efficiency and Low Emissions: Retort systems recycle gases and heat, leading to higher efficiency (charcoal yield around 35-40%) and lower emissions.
- Consistent Quality: Offers more consistent temperature control, resulting in high-quality, uniform charcoal.
- Scalable: Retort kilns can be scaled up for industrial use, providing a bridge between small-scale and larger commercial production.
- Higher Cost: Initial investment is higher, making it suitable for producers focused on higher output and quality.
Continuous Pyrolysis Reactors
- Description: These reactors continuously feed biomass into a pyrolysis chamber, where it undergoes controlled carbonization in an oxygen-limited environment.
- Scope:
- Industrial-Scale Production: Suitable for large-scale, continuous charcoal production due to automation and high efficiency.
- High Energy Efficiency: Recovers and reuses released gases for energy, reducing external fuel needs.
- Environmental Benefits: Designed with low-emission technology to reduce pollutants significantly.
- High Quality and Consistency: Produces uniform, high-quality charcoal or biochar suitable for commercial and industrial applications.
- High Initial Cost and Technical Requirements: Requires technical expertise and a substantial initial investment.
Gasifier Systems
- Description: Biomass is partially combusted in a gasifier to produce a mix of syngas and a charcoal byproduct.
- Scope:
- Dual Benefit: Generates syngas (a clean fuel) alongside charcoal, making it suitable for both energy production and charcoal output.
- Medium Scale: Suitable for medium-scale applications like farms or small industries that can benefit from both syngas and charcoal.
- Moderate Efficiency and Emissions: Efficiency varies, and emissions are moderate compared to pyrolysis reactors.
- Requires Expertise: Involves a more complex process and needs expertise in gasification technology.
Solar-Powered Carbonization
- Description: This emerging technology uses solar heat to carbonize biomass in a controlled chamber, reducing reliance on external fuel.
- Scope:
- Eco-Friendly: Uses renewable solar energy, making it highly sustainable with near-zero emissions.
- Limited by Climate: Best suited for areas with strong and consistent sunlight, as cloudy conditions can interrupt the process.
- High-Quality Charcoal: Can produce high-quality charcoal, though production rates are currently low.
- Experimental Stage: Still in development and not widely adopted; may require technological advancements to be commercially viable.
Comparative Scope and Applications of Charcoal-Making Methods
Method | Efficiency | Cost | Emissions | Scale | Charcoal Quality | Applications |
---|---|---|---|---|---|---|
Pit and Earth Mound | Low | Low | High | Small | Low to Moderate | Small farms, traditional rural areas |
Metal Drum Kiln | Moderate | Low | Moderate | Small | Moderate | Small farms, rural community use |
Retort Kiln | High | Moderate | Low | Medium | High | Small to medium commercial production |
Continuous Pyrolysis | Very High | High | Very Low | Large | Very High | Industrial-scale, commercial biochar |
Gasifier | Moderate | Moderate | Moderate | Small-Medium | Moderate | Farms, small industries, energy + charcoal |
Solar Carbonization | Variable | Moderate | Very Low | Small | High | Eco-focused farms, experimental |
Traditional Pit or Trench Method
- Process: Dig a pit or trench in the ground, place biomass in it, and cover it with soil, leaving some ventilation holes.
- Burning: Ignite the biomass and allow it to burn slowly, with restricted airflow, to facilitate carbonization.
- Duration: 2-5 days, depending on biomass quantity and moisture content.
- Pros: Low-cost setup, minimal equipment required.
- Cons: Low yield, moderate control over charcoal quality, high emissions.
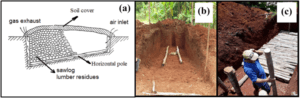
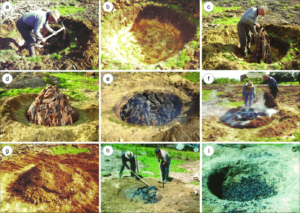
Earth Mound Kiln
- Setup: Construct a mound with biomass, then cover it with soil or clay to limit oxygen flow.
- Carbonization: Biomass inside the mound slowly carbonizes over 3-5 days.
- Control: Small openings at the top help release gases and control the burn.
- Pros: Low investment cost, suitable for small-scale production.
- Cons: High labor requirement, low efficiency, and high emissions.
The Earth Mound Kiln is a traditional, low-cost method for making charcoal, especially suitable for small-scale production on farms using agricultural biomass. Here’s a detailed overview of the process and its advantages and disadvantages:
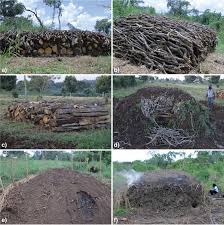
Steps to Build and Operate an Earth Mound Kiln
- Site Selection and Preparation:
- Choose a flat, open area for building the kiln to ensure safety and ease of access.
- Clear the area of any flammable material to reduce the risk of accidental fires.
- Gathering Biomass:
- Collect dry agricultural biomass such as crop residues, branches, leaves, and other organic matter.
- Ensure the biomass is dry; wet biomass takes longer to carbonize and reduces efficiency.
earth mound kiln carbonization method
- Building the Mound:
- Pile the Biomass: Place the biomass in a mound shape. The size of the mound can vary, but typical dimensions are 1-2 meters high and 2-3 meters in diameter.
- Layering: For more efficient carbonization, stack smaller, more flammable materials at the bottom and larger pieces toward the top.
- Covering the Mound:
- Cover the mound with a layer of moist soil or clay, approximately 5-10 cm thick.
- Leave small ventilation holes at the base to control airflow and allow gases to escape.
- Ignition:
- Start a fire at the base of the mound through one of the ventilation holes.
- Once the fire is going, partially seal the hole to limit oxygen. The biomass will begin to carbonize in the low-oxygen environment.
- Controlling the Burn:
- Monitor the mound regularly. If flames break through the soil cover, patch the area to prevent too much oxygen from entering.
- Adjust the ventilation holes as needed to keep the process smoldering rather than burning vigorously.
- Completion:
- The process can take anywhere from 3 to 5 days, depending on the size of the mound and the biomass moisture content.
- When carbonization is complete, the mound will cool, and no more smoke will be emitted. Cover all ventilation holes to extinguish any remaining embers and let the mound cool for a day or two.
- Harvesting the Charcoal:
- Once the mound has cooled completely, remove the soil layer and harvest the charcoal.
- Crush or sieve as needed, depending on the intended use.
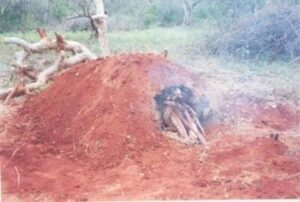
Advantages of the Earth Mound Kiln
- Low-Cost Setup: Requires no special equipment; basic materials like soil or clay are sufficient.
- Adaptable: Can use various types of agricultural biomass and be scaled to different mound sizes.
- Easy to Operate: Suitable for rural areas with limited resources, making it accessible for small farms.
Disadvantages of the Earth Mound Kiln
- Low Yield: Earth mounds are generally less efficient, with a charcoal yield of about 15-25% of the original biomass.
- Labor-Intensive: Building, monitoring, and patching the mound require consistent labor.
- High Emissions: Generates smoke and other emissions, which can contribute to air pollution and health risks if done on a large scale or without adequate ventilation.
- Variable Quality: Hard to control temperature and oxygen levels, which can result in uneven quality of charcoal.
Tips for Better Results
- Dry Biomass Thoroughly: Dry biomass carbonizes more evenly and quickly.
- Control Moisture in Covering Soil: A slightly damp cover helps prevent the soil from catching fire while still allowing gases to escape.
- Ensure Adequate Ventilation: Balance airflow to maintain a slow, smoldering burn rather than open flames.
This method has been used for centuries due to its simplicity and accessibility, making it a viable option for farm-based charcoal production. However, for larger-scale, cleaner, and more efficient charcoal production, considering a kiln with more control over combustion and emissions may be beneficial.
Metal Drum Kiln (Oil Drum Method)
- The Metal Drum Kiln, also known as the Oil Drum Method, is a practical, low-cost approach for producing charcoal on a small scale.
- It’s more efficient and controlled than traditional methods like the Earth Mound Kiln, while remaining affordable and portable.
- Here’s a step-by-step guide to setting up and operating a Metal Drum Kiln:
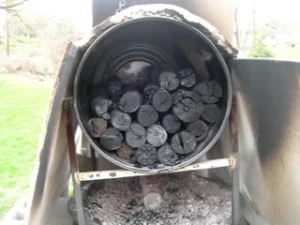
Materials and Tools Needed
- Metal drum: Typically a 200-liter (55-gallon) metal drum.
- Biomass: Dry agricultural waste such as crop residues, branches, leaves, or wood.
- Lid and small metal pipes (optional): For better control over airflow and to create a chimney effect.
- Shovel and water: To seal and extinguish the kiln at the end.
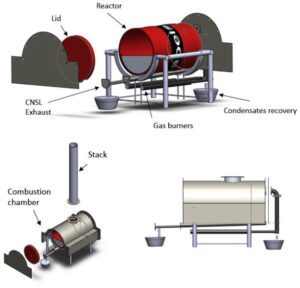
Steps to Make Charcoal with a Metal Drum Kiln
- Preparing the Drum:
- Drill or cut a series of small holes (2-3 cm diameter) around the bottom of the drum to allow for airflow.
- Cut larger holes on the lid or sides for ventilation.
- A few holes on the lid can act as a chimney, which helps with airflow and even carbonization.
Biomass charcoal making in the drum
- Filling the Drum with Biomass:
- Place small, easily flammable material at the bottom of the drum.
- Fill the rest of the drum with dry agricultural biomass, layering larger and denser pieces toward the top. Filling loosely helps air circulate through the biomass.
charcoal making from drum with wooden rods
- Ignition:
- Start the fire at the bottom through the ventilation holes or by lighting the material inside from the top.
- Let the fire burn with ample airflow at the start to ignite all layers.
- Controlling the Burn:
- Once the fire is established, close the lid if possible, leaving a few small openings to limit oxygen intake.
- The drum will begin to smolder as the fire consumes available oxygen. This slow-burning process (carbonization) turns the biomass into charcoal.
- Adjust the airflow by partially blocking the lower ventilation holes if flames get too vigorous. The goal is a slow, steady burn without large flames.
- Completion of Carbonization:
- The process typically takes 4-6 hours, depending on the biomass moisture content and size of the drum.
- When the smoke becomes thin and blue (instead of thick and white), the carbonization is nearing completion.
- Seal all holes to cut off oxygen supply and stop the burn. Let the drum cool completely, which can take several hours or overnight.
- Harvesting the Charcoal:
- Once cooled, remove the lid and extract the charcoal.
- If needed, crush or sieve the charcoal based on its intended use (e.g., biochar, fuel, filtration).
Advantages of the Metal Drum Kiln
- Cost-Effective: Requires minimal setup and uses commonly available materials.
- Portable and Reusable: The drum is easy to move, making it suitable for small-scale operations.
- Controlled Carbonization: Better control over airflow compared to earth kilns results in more uniform and higher-quality charcoal.
- Cleaner than Traditional Kilns: Emits less smoke and harmful gases compared to earth mounds.
Disadvantages of the Metal Drum Kiln
- Limited Capacity: Only produces a small amount of charcoal per batch due to the drum’s limited volume.
- Requires Monitoring: Needs regular checking and adjusting of airflow to ensure efficient carbonization.
- Moderate Efficiency: Charcoal yield is higher than traditional methods but lower than advanced kilns like retort or brick kilns.
Tips for Efficient Charcoal Production
- Use Dry Biomass: Wet or green biomass prolongs the process and lowers charcoal quality.
- Monitor Airflow: Adjust ventilation holes as needed to avoid over-burning and maximize charcoal yield.
- Recycle Heat and Gas (Optional): In some designs, you can capture and recycle the gases released during pyrolysis for a cleaner burn.
Variations of the Metal Drum Kiln
Adding a second drum or creating a double-barrel system can help capture more heat and increase efficiency. In this setup, the inner drum holds the biomass, while the outer drum serves as an insulator and collector of released gases.
The Metal Drum Kiln is a versatile method that allows for straightforward, portable charcoal production, making it ideal for small farms and rural settings.
Retort Kiln
- Setup: This involves two chambers: a primary one for biomass and a secondary chamber for burning released gases.
- Operation: Heat the biomass in the primary chamber without oxygen, using gas from the secondary chamber for continuous heat.
- Duration: Faster carbonization than traditional methods.
- Pros: Higher yield and efficiency, reduces smoke and emissions.
- Cons: Higher initial investment and more complex setup.
Biochar Reactors (Continuous and Batch Pyrolysis)
- Process: Use pyrolysis reactors specifically designed to convert biomass to biochar.
- Technology: Pyrolysis occurs in an oxygen-limited environment at high temperatures.
- Continuous Systems: These can process large volumes efficiently.
- Pros: High-quality charcoal, energy-efficient, controlled emissions.
- Cons: Requires investment in equipment and technical knowledge.
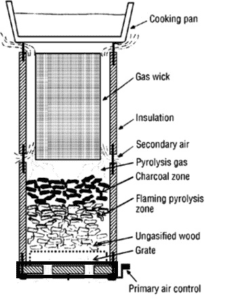
Gasifier System
- Function: Gasification is a form of partial combustion that produces a charcoal byproduct.
- Setup: Biomass is fed into a gasifier, which uses controlled airflow to create syngas while leaving charcoal residue.
- Pros: Dual benefit of syngas for energy and charcoal as a byproduct.
- Cons: Requires technical expertise and significant investment.
Conclusion
- Each method for charcoal making has distinct benefits and limitations, ranging from basic, low-cost options to high-efficiency, scalable systems.
- For sustainable development, there’s an ongoing shift towards methods that balance efficiency, low emissions, and quality.
- Emerging and advanced technologies, such as continuous pyrolysis and solar-powered carbonization, promise environmentally friendly alternatives to traditional methods, suitable for both small- and large-scale applications.
Â